AirShock The Most Effective Technology for Water Well Rehabilitation
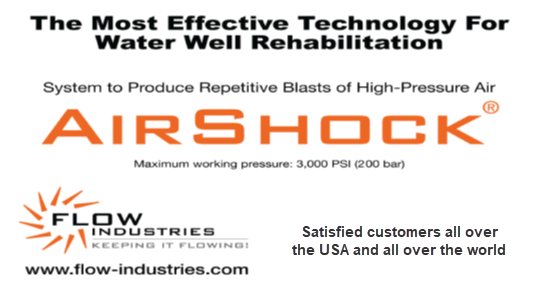
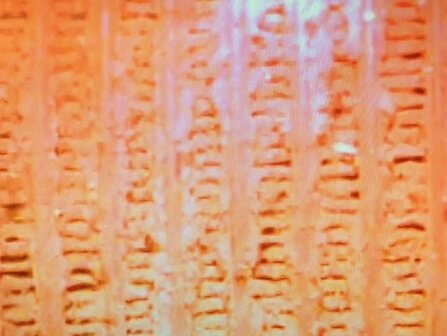
Before AirShock treatment.
– Highly Effective for both screened and open wells.
– Relatively short procedure
– Used independently or combined with chemicals
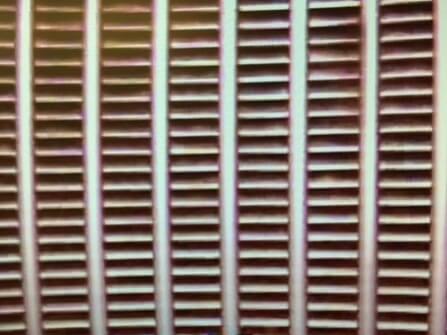
After AirShock treatment.
– Safe and environmentally friendly.
– Short well downtime.
– No royalties, no minimums.
USA and foreign patents
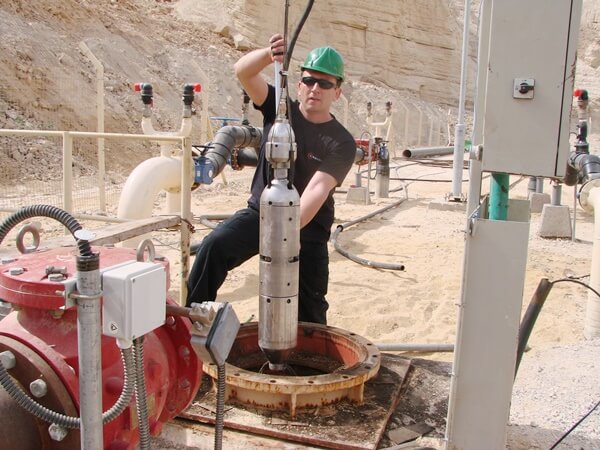
Running AIG into the well
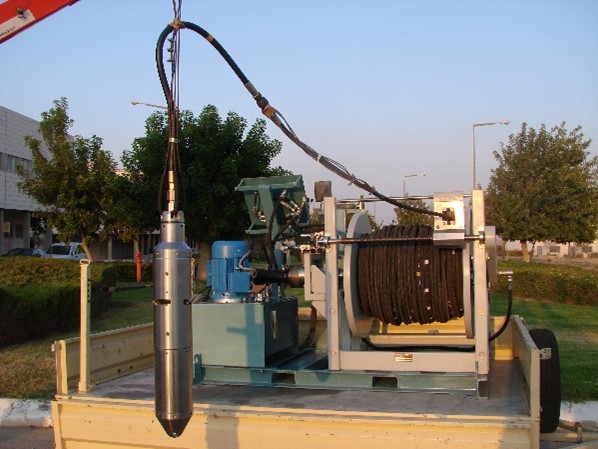
AirShock system
For further information, please call: +1 (484) 893-0085
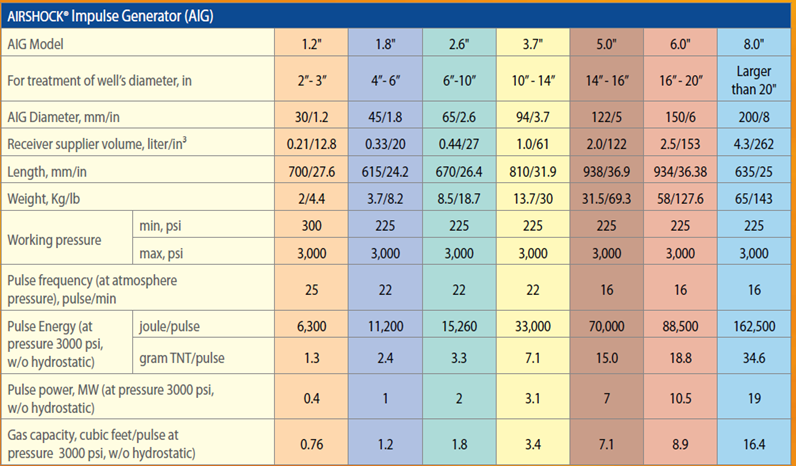
AIRSHOCK® is an innovative, non-destructive and environmentally friendly technology for water well rehabilitation and development. AIRSHOCK® is based on the compressed gas continuous accumulation and its repeated sudden pulsing release in the well by means of the AIRSHOCK® Impulse Generators (AIGs). The process involves creation of a shock wave and oscillating gas bubble after each pulse resulted in removing hardened scale and biological build-up from the screen, gravel pack and surrounding area. The shock wave breaks up the scale on the screen, while the expanding and contracting bubble forces water in and out of the gravel pack and aquifer ensuring a comprehensive washing process. In a very short time, a well is completely restored to the original level of efficiency. The method is unique both in success and ease of setup and operation.
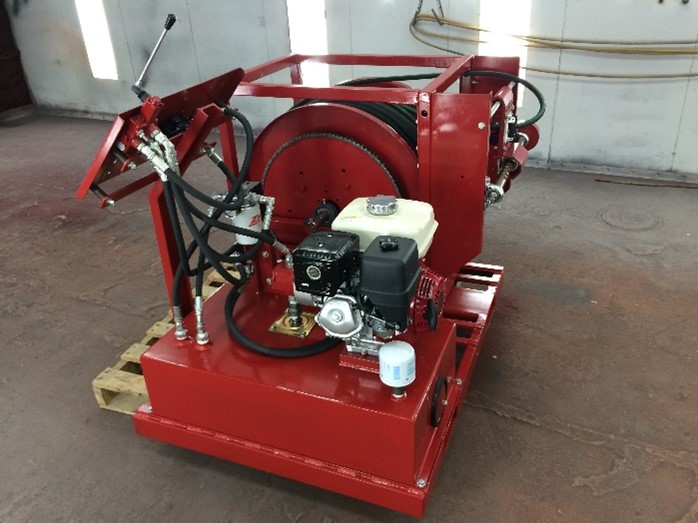
AirShock Hose Reel
The AIRSHOCK® Impulse Generator provides the comprehensive treatment of each single foot of the screen as being gradually moved down-up and up-down in the well.
We provide contractors with a complete AIRSHOCK® system including:
- AIRSHOCK® Impulse Generator (AIG) (choice of 7 different sizes)
- Hose reel + Control Panel
- Hose
- Contractor needs to get supply of standard nitrogen or air high-pressure bottle for each job.
2024 Groundwater Week
Booth # 261
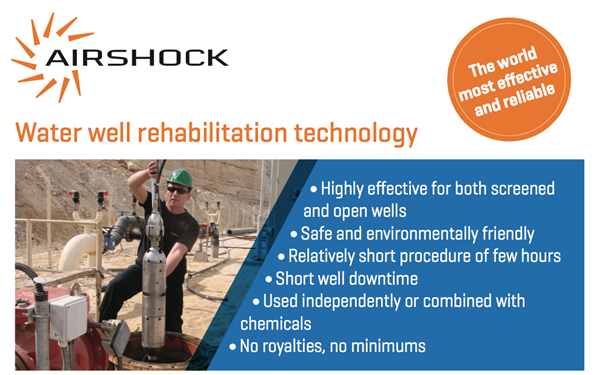
Call Now : +1 (484) 8930085
The concept behind AIRSHOCK® is the rapid release of high-pressure gas. This creates a high energy percussive wave and oscillating gas bubbles that dislodge particulate matter and scale buildup as well as displace the surrounding water. Three things happen when the AIG fires. First is the shock wave creation that blasts mineral scale, rust and biological buildup from the inside and between the openings of the well screen. Second, expanding and contracting bubbles force water in and out of the gravel pack and aquifer ensuring a washing process. Third, the pulse results in in a low-pressure area under the AIG tool and vacuuming the fines from the gravels back into the well. AIRSHOCK® has four main applications:
1. Dislodging and removing buildup from inside the screen wall.
2. Delivering chemicals through the screen and into the gravel pack and formation.
3. Developing fines and filter cake from new wells.
4. Stabilizing gravels in the gravel packs thereby removing voids in the gravel pack.
Along with high efficiency, the advantage of the system is ease of use. AIRSHOCK® consists of a small complement of equipment that may be transported on a small trailer pulled by a pickup or a truck and operated by one person. Setup time is typically under an hour. Assuming two shots per foot (6-8 second), a 100-foot screen section may be treated with one pass in about 15 minutes. Two or three passes are typically made. The operator has full control of the energy delivered to the well. He selects the size of the tool to use based on the diameter of the well and has control of the pressure applied up to 3,500 psi. The well may be treated repeatedly if necessary. The AIG is lowered into the well on a double braided high-pressure hydraulic-pneumatic hose spooled on an electric or hydraulic hose reel. Depending on the chemistry of ground water the high-pressure gas may be either nitrogen or air. In the special cases carbon dioxide may be used. In most cases the gas of the choice is nitrogen since it will not cause oxidation or contribute to aerobic bacteria growth. It is readily available at most job sites.
Pressures may be varied from a few hundred psi up to 3,000 psi. The AIG diameter and gas pressure should be chosen to meet well diameter its condition and treatment requirements.
Air lifting or pumping is recommended in conjunction with airshocking to remove materials before they have a chance to settle.
AIRSHOCK® may be used to agitate chemicals in the well, i.e. add chemicals to the well and
AIRSHOCK, let set over night and AIRSHOCK® again before pumping out.
The AIRSHOCK® system does not require special permitting or handling requirements for operation.
‘
AIG above the water well
Ease of use
Along with high efficiency, the advantage of the system is ease of use. AirShock® consists of a small complement of equipment that may be transported on a small trailer pulled by a pickup or a truck and operated by one person. Setup time is typically under an hour. Assuming two shots per foot (6-8 second), a 100-foot screen section may be treated with one pass in about 15 minutes. Two or three passes are typically made. The operator has full control of the energy delivered to the well. He selects the size of the tool to use based on the diameter of the well and has control of the pressure applied up to 3,000 psi. The well may be treated repeatedly if necessary. The AIG is lowered into the well on a double braided high-pressure hydraulic-pneumatic hose spooled on an electric or hydraulic hose reel.
Revolutionizing Hopper Maintenance in Cement Production with AirMace Air Cannon
In the dynamic world of cement production, operational efficiency and workplace safety are crucial. One of the most significant advancements in hopper maintenance is the successful implementation of the AirMace air cannon system, particularly in the Cement Production Division. This innovative solution not only improves productivity but also enhances safety for workers.
A Game-Changer for Hopper Maintenance
The Cement Production Division recently celebrated the successful installation of the AirMace air cannon, equipped with a booster, designed to eliminate hopper clogging in a safer and more efficient manner.
Traditionally, workers faced hazardous and labor-intensive methods to clear blockages. These methods involved chisels, hammer drills, and physical labor while being exposed to hot clinker reaching temperatures of 300°C—a process both dangerous and time-consuming.
The Installation Process
Led by the dedicated division engineer, the installation involved:
1. Mounting the Air Cannon: Positioned on a specially designed mount.
2. Metal Pipe Integration: Connecting the cannon to a metal pipe that fits seamlessly into a 4-inch sleeve.
3. Boosting Pressure: Utilizing the AirMace booster to elevate the line pressure from 6 bar to an impressive 11 bar.
This meticulous setup ensures the hoppers beneath the 90,000-ton clinker silo remain unclogged with minimal manual intervention.
Enhanced Safety and Efficiency
The new AirMace air cannon system has transformed hopper maintenance by:
• Eliminating Worker Exposure: Workers no longer need to endure hazardous conditions or handle cumbersome tools near hot clinker.
• Speeding Up Processes: Maintenance is now significantly faster and more reliable.
• Improving Operational Safety: Reducing workplace risks with automated, high-pressure solutions.
Conclusion
The AirMace air cannon installation represents a groundbreaking advancement for the Cement Production Division. This innovative solution sets a new benchmark for safety and efficiency in industrial operations.
Stay tuned as we continue to explore and implement cutting-edge technologies to revolutionize cement production processes.